The porcelain tile is a clay body composition with the conventional triaxial kaolin-feldspar-quartz components. Firstly, upon heating, the drying of the clay body occurs at about 100°C. Any residual water is eliminated at this point. At the temperature range of 500°C to 600°C, the water of crystallisation mainly in the silicate layers is removed by the reaction producing metakaolin Al2Si2O6 from kaolin Al2Si2O5[OH]4 [1,2]. The gas pressure may produce a volume expansion and the heating rate must be carefully controlled for bodies containing substantial amounts of clay. Between 300°C to 700°C, any organic material present in the body whether as part of the material or binder will burn off.
After this, no changes can be observed until about 950°C. This is when the metakaolin clay phase undergoes an exothermic reaction and decomposes to the spinel phase and amorphous SiO2 [3]. The exact structure of the spinel phase is controversial. The spinel phase composition was previously thought to be 2SiO2.3Al2O3 or γ - Al2O3 [3,4]. However, in a study conducted by Okada et al [3], the spinel phase was determined to be nearly all of Al2O3 with about 8% SiO2. Therefore, in summary, there are still some uncertainties regarding the exact structure of the spinel phase. When the porcelain tile is fired until about 1000°C - 1100°C, a boundary reaction of the silica and feldpsar begins and a melt is formed. During the heating, needle like mullite crystals crystallize at relatively low temperatures from this melt [5].
The firing of the highly vitrified porcelain tile depends on the reactivity of the meta-kaolin components and the feldspar's sintering action at certain temperatures which control the body component reactions that produce the amorphous glassy phase. The development of new phases, the temperature of the onset of the melt formation and the glass-phase viscosity depend on the type of feldspar and more importantly the alkali ratio used.
There are two types of mullite formed. The mullites can be distinguished by their size. One of them is the primary mullite (< 0.5µm) which appears to be scaly as compared to the other more well known needle type mullite. The primary mullite originates from kaolin or clay in the batch by a solid state reaction. It forms at a lower temperature and is the product of the clay minerals. The needle type mullite (> 1µm) can be referred to as the secondary mullite and are formed with the assistance of the melt by dissolution and re-crystallisation of alumino-silicates when feldspar is added to the batch. The main differences between the primary and secondary types of mullite are the size, shape and degree of aggregation of the mullite crystals [4,5,6]. Figure 1 and 2 illustrates by SEM the two types of mullite.
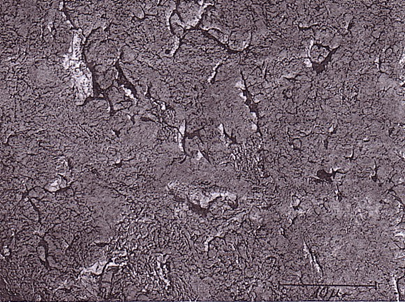
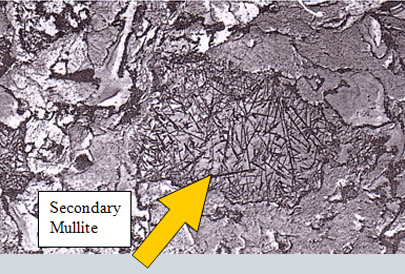
The SEM micrograph (Figure 3) shows the different phases of a porcelain tile body. During firing the main crystalline phases corresponding to the mineral such as feldspar in the unfired body disappear. New crystalline and amorphous phases are developed. The phase composition of the porcelain tile body consist of the newly developed phases namely interlocked crystals of mullite and amorphous phase and residual phases present in the original unfired body namely quartz and feldspar. Only a small amount of quartz dissolves in the melt during firing while the rest remains unreacted. Figure 4 shows the feldspar relict while Figure 5 shows the unreacted quartz in L1. Relict is a geological term indicating that the particular grain was that mineral in the unfired body, although it has been altered by firing. A small number of pores are also present in the porcelain tile body [7,8].
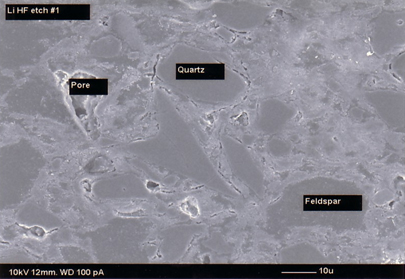
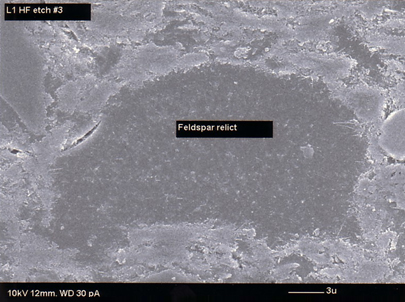
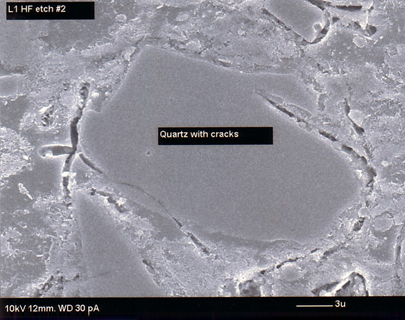
It is a widely accepted hypothesis that the strength of the porcelain is caused or greatly increased by the feltlike interlocking of the mullite needles. This theory is known as the mullite hypothesis. The mechanical strength of the porcelain tile depends on the amount of secondary mullite needles. A higher mullite content contributes to a higher mechanical strength [1,9].
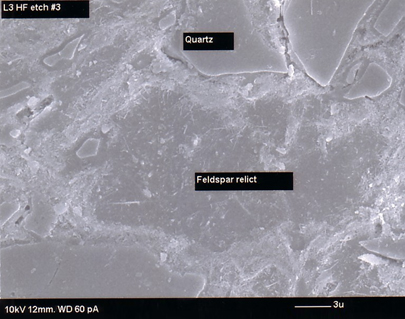
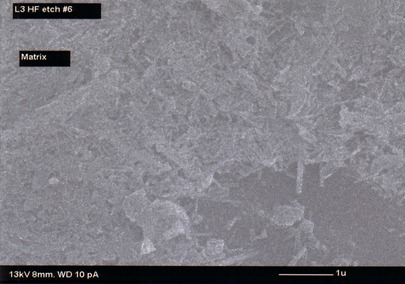
The other theory to explain mechanical strength is the matrix reinforcement hypothesis [9]. There is a fair amount of residual quartz particles as only a small portion dissolves in the melt. These residual quartz particles can be observed in Figure 3 and more clearly in Figure 5. These unreacted quartz crystals have a higher coefficient of thermal expansion than the surrounding matrix (glassy phase). The strong compressive stresses on the glassy phase cause strength improvements of the porcelain body.
- Carty, W.M.; Senapati, U. "Porcelain - Raw Materials, Processing, Phase Evolution and Mechanical Behaviour" J. Amer. Ceram. Soc., 81, pp.3-20 (1998)
- Schmidt, H. "Chemical and Physical Reactions in heavy clay bodies during firing" Ziegelindustrie International, pp. 367-397( June/July1981)\
- Okada, K.; Otsuka, N.; Ossaka, J. "Characterisation of Spinel Phase Formed in The Kaolin-Mullite Thermal Sequence" J. Amer. Ceram. Soc., 69, pp.C-251-C-253 (1986)
- Iqbal, Y.; Lee, W.E. "Microstructural Evolution in Triaxial Porcelain" J. Amer. Ceram. Soc., 83[12], pp.3121-27 (2000)
- Schuller, K.H. "Reactions Between Mullite and Glassy Phase in Porcelains" Trans. Br. Ceram. Soc., 63, pp.
102-117 (1964) - Lundin, S.T. "Studies on Triaxial Whiteware Bodies" Almqvist & Wiksell/ Stockholm, pp.69-91 (1959)
- Manfredini, T. "Porcelainized stoneware: processing and characteristics" International Ceramics Journal, pp.61-64 (August 2002)
- Dondi, M.; Fabbri, B.; Pellacani, G.C. "Microstructure and Mechanical Properties of Porcelainized Stoneware Tile" Fourth Euro Ceramics - Vol.11, pp. 319-326 (1995)
- Mattyasovszky-Zsolnay, L. "Mechanical Strength of Porcelains" J. Amer. Ceram. Soc., 40[9], pp.299-306 (1957)
- Mörtel, H. "Influence of the batch composition on the reaction behaviour and Properties of Fast fired(2h) Porcelain" Science of Ceramics 9, pp.84-91(1977)